When to HR with AI (and When Not To)!
Are you tired of dealing with inconsistent and inefficient near-miss incident reporting in your manufacturing company? You're not alone.
The manufacturing industry is full of potential hazards, making it crucial to be proactive in identifying and addressing risks. One key aspect of managing workplace safety is reporting near misses. When your employees can quickly and easily report near-miss incidents, you'll have valuable data at your fingertips, allowing you to analyze trends and implement preventive safety measures.
Our easy-to-use near-miss incident report template is designed to simplify this process for you. Simply download the form, print it out, and you're good to go! This handy form will not only help you gather crucial information about near misses but also promote a culture of safety and continuous improvement within your organization. So, let's dive in and explore how our free downloadable near- miss report form can benefit your manufacturing company!
Download Our Free Near-Miss Report Form
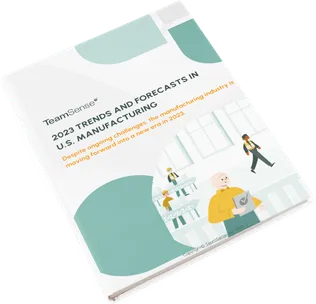
Enter your company email below to get instant access to the template.
What is a near-miss incident?
A near-miss incident, also known as a close call or near hit, is an unplanned event that doesn't result in injury, illness personal injury, or property damage but had the potential to do so. In the manufacturing industry, these events can provide valuable insights into potential hazards and opportunities for improvement. By paying close attention to near misses, you can take proactive steps to prevent future accidents and maintain a safe working environment.
Definition and examples
To paint a clearer picture, let's consider some examples of near-miss incidents in a manufacturing setting:
- An employee narrowly avoids being struck by a falling object because they stepped away just in time.
- A machine malfunctions but stops before causing any damage or injury.
- A forklift operator comes close to hitting a pedestrian but manages to stop in the nick of time.
Importance of identifying and reporting near misses
Near-miss reporting is vital for several reasons. First, it helps identify potential hazards that may have been overlooked during routine safety inspections. Second, it encourages employees to stay vigilant and be proactive in spotting risks, fostering a culture of safety. Lastly, near-miss reporting provides valuable data for management to analyze and use in implementing preventive measures to reduce the likelihood of future accidents.
Key components of a near-miss incident report form
A well-structured near-miss incident report form helps ensure that important information is captured and communicated effectively. Our free downloadable near miss report template includes the following key components:
Incident details (date, time, location)
It's essential to record the date, time, and location of the near miss events, as this information helps identify patterns and trends related to specific areas or times of the day. This data can be invaluable in directing targeted safety improvements and interventions.
Description of the near miss
A clear, concise description of the near miss is crucial for understanding the circumstances and potential hazards involved. Encourage employees to provide a near miss report in as much detail as possible, including the sequence of events, contributing factors, potential hazard, and any equipment or materials involved.
Involved parties and witnesses
Include the names and roles of any individuals directly involved in the near miss events, as well as those who witnessed the incident. These individuals may provide valuable insight into the event and help identify opportunities for improvement.
Root causes and contributing factors
Understanding the root causes and contributing factors of a near miss is vital for implementing effective preventive measures. Employees should be encouraged to think critically about why the incident occurred and identify any underlying issues that may need to be addressed.
Immediate corrective actions taken
Recording any immediate corrective actions taken following the near miss, such as shutting down a machine or clearing a blocked walkway, is important for demonstrating your company's commitment to safety and continuous improvement.
Recommendations for future prevention
Lastly, the report should include any recommendations for preventing similar incidents in the future. This may involve changes to procedures, additional training, or equipment upgrades. Encourage employees to think creatively about potential solutions and be open to their suggestions. This collaborative approach can help foster a strong safety culture within your organization.
Effortless Attendance Tracking, Just a Text Away
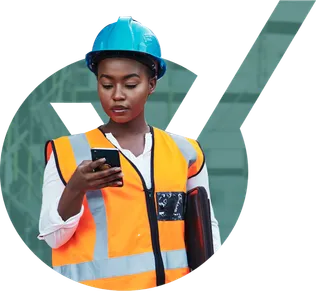
See how TeamSense saved HelloFresh 3-4 hours per day managing attendance through text. Read the case study here and book your demo today!
How to report a near-miss incident using our template
Our user-friendly near-miss incident report template makes it easy to document and report near misses in your manufacturing company. Here's a step-by-step guide on how to use the template effectively:
Downloading and printing the near-miss reporting form PDF
To get started, simply click the download link provided in this blog post. The near-miss reporting form is in a PDF format, ensuring it's easy to print and accessible across various devices. Once downloaded, print out a sufficient number of copies to have on hand in your workplace, and save them so employees can easily access them whenever needed.
Completing the form with accurate information
When a near miss occurs, prompt the involved employees or witnesses to contact you to complete the form as soon as possible. Timely reporting ensures that details are fresh in their minds and increases the accuracy of the information provided. Encourage employees to be thorough and honest in their descriptions, focusing on facts rather than opinions or blame.
Submitting the completed form to the appropriate personnel
Once the form is completed, it should be submitted to the designated safety officer, supervisor, or manager, depending on your company's specific reporting structure. This individual will be responsible for reviewing the report, following up on any necessary actions, and ensuring the incident is properly documented and tracked.
By consistently using our near-miss incident report template, your manufacturing company can improve the efficiency and effectiveness of near-miss reporting, enabling you to identify trends, address potential hazards, and foster a culture of safety throughout your organization.
-
Ideally, the person directly involved in the near miss or a witness should complete and sign the form. If neither is available, a supervisor or safety officer can fill out and sign the form based on information gathered from those involved or from the scene of the incident.
-
A near miss should be reported as soon as possible, preferably within 24 hours of the incident. Reporting an accident in a timely manner ensures that details are still fresh in the minds of those involved and can help prevent similar incidents from occurring in the future.
-
Regularly review and analyze near-miss reports to identify patterns and trends in your workplace. Use this information to prioritize safety improvements, make changes to processes or equipment, and provide targeted training for employees. Sharing anonymized near-miss data with your workforce can also help raise awareness of potential hazards and encourage a culture of safety.
-
Create a positive reporting culture by emphasizing the importance of near-miss reporting for overall workplace safety. Ensure employees understand that reporting near misses is not about assigning blame, but about learning and improving. Provide training on how to identify and report near misses, and recognize or reward employees for their participation in the reporting process.
Automated attendance tracking. One text away.
Bye-bye archaic call-off solutions. Hello, automated attendance.
Record call-offs with text and alert managers in real-time.
Focus on your team, not spreadsheets.