When to HR with AI (and When Not To)!
In this post, we’ll share key takeaways from earnings calls, highlight emerging trends, and break down the differences across sectors like automotive and food & beverage.
1. The Labor Situation: A Widespread Concern
It’s no surprise that labor planning challenges are still top of mind for manufacturers. Companies across the board are facing difficulties in hiring and retaining skilled workers. The labor shortage is causing a ripple effect, impacting production timelines and operational efficiency.
What the Earnings Calls Show:
Skilled Labor Shortage: 85% of companies we analyzed mentioned challenges in hiring or retaining skilled workers.
Training & Retention Efforts: 60% of manufacturing leaders are investing in training programs or offering higher wages to attract talent.
Sector Differences:
Automotive Industry: 90% of automotive companies reported challenges with labor, especially in skilled technical roles. Automation is a key focus as they look for ways to reduce reliance on manual labor.
Food & Beverage: While labor shortages were still a concern (75%), the focus here was more on improving worker safety and increasing workforce diversity.
2. Supply Chains: Still Navigating the Storm
While the supply chain bottlenecks of the last few years have eased, manufacturers are still dealing with delays, cost increases, and unpredictable disruptions. Companies are becoming more strategic about their supply chains, focusing on diversification and resiliency.
What the Earnings Calls Show:
Supply Chain Diversification: 70% of companies are moving towards multiple suppliers to reduce reliance on single sources.
Nearshoring: 45% of companies are actively nearshoring or considering it to shorten supply chains and reduce risk.
Sector Differences:
Automotive Industry: A major shift is happening here, with 80% of automotive companies focusing on nearshoring to minimize supply chain disruptions from overseas suppliers.
Food & Beverage: 55% of food & beverage companies are diversifying suppliers, but many are focusing more on local sourcing to improve sustainability efforts

The Costly Impact of Absenteeism on Manufacturing Operations
Learn how chronic, unplanned absenteeism is a costly impediment to manufacturing productivity and efficiency, and how you can reduce absenteeism.
3. Mixed Signals on Demand: Cautious Optimism
Demand forecasts are a mixed bag. While some sectors show growth potential, others are feeling the pinch due to economic uncertainty and inflation. Manufacturers are being cautious in their projections, yet many remain hopeful about recovery in the second half of 2024.
What the Earnings Calls Show:
Optimistic Demand Growth: 55% of companies report stable or growing demand in their key markets.
Cautious Forecasting: 45% are revising their demand forecasts down, mainly due to inflation concerns and geopolitical uncertainty.
Sector Differences:
Automotive Industry: Unlike some other sectors, automotive demand is subdued. Leaders like Lear Corp. and Dana Inc. highlighted muted vehicle demand, with Lear implementing cost-cutting measures and Dana trimming engineering budgets. This cautious outlook reflects ongoing supply chain pressures and fluctuating consumer interest, particularly in traditional vehicles.
Food & Beverage: On the other hand, food & beverage manufacturers are feeling more cautious, with only 45% seeing strong demand. Inflation and shifting consumer preferences are making forecasting harder.
What It Means for You:
At TeamSense, we believe that addressing these challenges starts with people. Whether it's improving communication across teams, streamlining operations, or finding new ways to engage your workforce, the right tools can make all the difference.
Our solutions are designed to help manufacturers tackle these issues head-on, whether you're managing labor challenges, optimizing supply chains, or navigating demand volatility.
Final Thoughts:
The manufacturing industry is anything but static. As we look ahead, the ability to adapt quickly and communicate effectively will be key. By staying informed and focused on building resilient teams, manufacturers can navigate uncertainty and come out stronger on the other side.
Want to learn more? Reach out to us to see how TeamSense can help streamline communication, engage your workforce, and support your manufacturing business.
About the Author
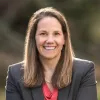
Sheila Stafford, CEO of TeamSense & AI in HR Innovator
As CEO of TeamSense, Sheila Stafford is at the forefront of transforming HR for frontline teams through AI-driven solutions. With a commitment to enhancing employee relations and simplifying workforce management, Sheila leads TeamSense in pioneering advancements that empower both frontline employees and HR teams. Her visionary approach combines cutting-edge technology with a thoughtful focus on enhancing human connection; Sheila strategically implements AI where it adds the most value while recognizing the critical role of personal interaction and ensuring that human engagement remains central when it matters most. Under her leadership, TeamSense is redefining how companies support and engage their frontline teams for a more connected, efficient workplace.